St Joseph’s Catholic High School have been serving our community of Workington and the surrounding areas for over 90 years providing quality education, pastoral support and advice/guidance to our students and their families and the local community.
St Joseph’s are a Good Catholic School according to our most recent OFSTED and Diocesan inspections and have a strong tradition of ensuring that students reach their desired next steps in employment or further education. The mission statement of the School is founded on: Living, Learning, Loving and Listening.
Multi Award Winning ASH Integrated Services were successful in securing this project as the main contractor via Arcadis Consulting UK (Ltd) who carried out the Tender Exercise. These works comprised of the replacement of fire alarm system in its entirety and emergency lighting adaptations, associated fire safety upgrades and fire doors, treatment of fire compartmentation.
ASH Integrated Services offers a joined up electrical, plumbing, heating, air conditioning and renewable energy project and maintenance solution, which reduces stress for clients by offering one point of contact and dedicated mechanical and electrical supervisors on each contract/project.
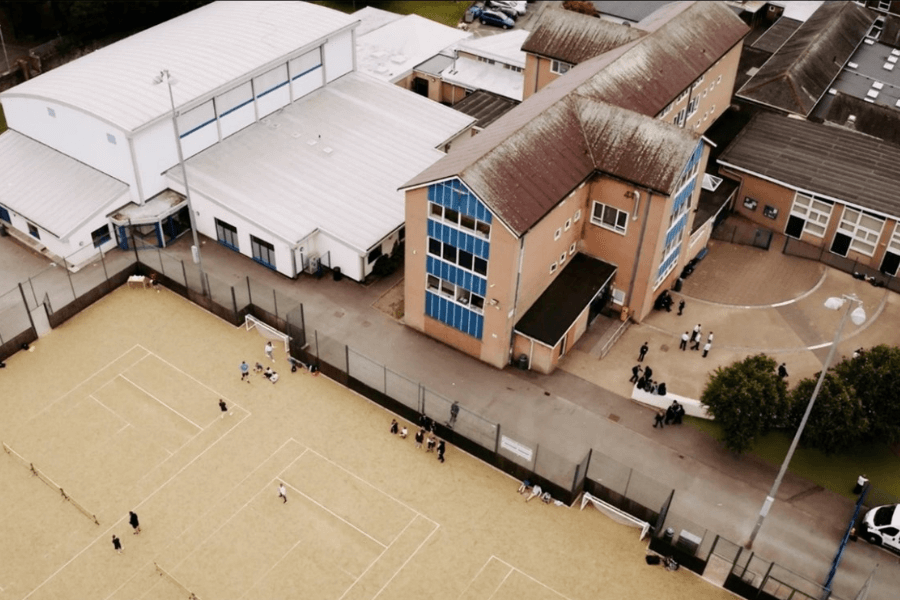
Principle Consultants:
These works were originally tendered via Mark Ruscoe – Senior Consultant, Arcadis Consulting (UK) Limited who also acted as the Project Manager for the project. We have previously carried out successful project works with Arcadis at the North Beckton Primary School, Milnrow Parish Church of England Primary School, Scarborough Sixth Form College, St Ignatius Primary School, St Martin’s C of E Primary School, St Joseph’s Primary School and Nelson St Phillips Primary School.
Projects and Project Management is a prime focus and area of competence within ASH Integrated Services where we have previously carried out similar successfully replacement Electrical Projects for our clients. We recognised an element of this project needed be delivered by Sub-Contractors such as Builders Works/Making Good and the Installation of the Fire Roller Shutters.
Our works included for the supply, installation, testing and commissioning together with the setting to work of the new installation. Working alongside and with our Sub-Contractors as ‘One Team’ we successfully delivered all aspects of the project, including design and build, installation and also maintenance if required after the project was completed.
Although we always aim to ‘Self-Deliver’ as many services as possible, using our directly employed Engineering Team. This helps us to keep costs under control and provide a consistently high level of quality and ‘First Class Service’.
Extent of Work – Electrical Building Services:
Removal of the Existing Services:
Generally, within the areas of works, the existing fire alarm system and emergency lighting was replaced in full. On completion of the works all of the old emergency lighting and fire alarm systems was stripped out in full. As part of our works we can confirm that all equipment was disposed of safely including all cabling, light fittings, socket outlets etc in accordance with the WEE directive.
Summary of Works Carried Out:
The work associated with this particular contract is for new fire alarm and emergency, lighting systems throughout the site at St. Joseph’s Catholic High School. The various aspects of work carried out as follows:
- General strip out of existing electrical services.
- Emergency lighting installations
- Fire alarm installations.
- Power installations to include
- Supplies to various fire panels.
- Supplies to emergency lighting gateways.
- Test and commission.
- As fitted drawings and manuals
- Demonstrations and instructions to end user for operation and maintenance procedures.
Electrical Distribution Installation:
We can confirm that the existing electrical distribution was retained in full and new protective devices were fitted to suit the proposed circuits. We also updated all labels, circuit labels, warning notices etc on appliances, switches, isolators.
Emergency Lighting and General Power Installation:
The emergency lighting and general power installations was carried out utilising single low smoke and fume cabling 6491B contained within suitably sized galvanised cable trunking and galvanised conduit systems to suit each environment. Generally, where mechanical protection is required a conduit system was used.
We can confirm that all final sub distribution circuits were provided with an additional earth continuity conductor, being sized the same size as the phase conductors. The power installations was also carried out on the ring main as indicated on the schedules provided.
Emergency Lighting Installation:
The emergency lighting for the site was designed in accordance with BS5266, Building Control Officer’s recommendations and discussion with the client on their operational needs for the building in the event of supply failure.
In general, emergency lighting was installed within the general lighting system for the building and utilise self-contained stand-alone emergency lighting bulkheads with internal battery packs to the luminaire and micro downlight type fittings (surface and recessed) plus high output batons to cover high risk areas. We can confirm that external emergency lighting were installed to all escape routes and local exit doors
We also supplied and installed self-test emergency luminaires in compliance with BS EN 50172 and BS EN 62034:2012 as part of the Thorlux Smartscan fully automated testing system. The system uses a wireless means of communication between devices to allow signalling of all test results and faults on the system. The fittings required a 230v connection from the local lighting circuit within each space and each luminaire is capable of automatically testing itself.
Fire Alarm Installation:
We carried out the supply, installation, testing and commissioning of a new fire alarm throughout the site including all equipment i.e. manual call points, automatic heat and smoke sensors, sounders, indicators, control panels, cables and the removal were necessary of the existing system.
The systems was designed to meet the requirement of the L2 standard in accordance with BS.5839 Pt1 2017. The systems comprised of the installation of Analogue Addressable Fire Detection system and control panels The main fire alarm panels was made by Advanced and open protocol using all components to form a complete system with all loop cards, interface units etc.
The installation was carried out utilising AEI Fire 2 core 1.5mm² screened /separate earth conductor with an overall red LSF sheath /cable installed in accordance with the various fire alarm loops indicated on the schematic diagram.
We can confirm that the Advanced Pro 5 Fire system, utilising Hoticki automatic detectors was fully commissioned by the systems specialist authorised to works on this system.
We also installed a dedicated 230v power supply from each buildings incoming electrical supply to the respective fire panel.
Control Panels:
The fire alarm control panels were mounted at a height that puts the display text at 1550mm AFFL. The panels were full compliant with EN54 parts 2, 4 & 13 with text display to indicate both the zone description and the exact location of the sensor, call point or interface raising the alarm.
The main panel was also fitted with an integral printer programmable for on-line or on demand printing. The panels came complete with integral batteries and charging circuit with the capacity to provide the system with 24 hours standby with ½ hour alarm load in the event of mains failure. The main panel also comprised of all the necessary facilities and equipment to automatically provide a suitable signal for transmission to a remote central monitoring station in order to call the Fire Brigade in the event of the fire alarm system going into “fire” status.
Manual Call Points:
All manual call points were installed with “push to break” safety glass with re-settable glass units. The call points were LPC approved to BS5839 parts 1 & 2 and raise the alarm within 3 seconds of being triggered.
Smoke Sensors:
The smoke sensors installed were low profile analogue addressable “optical” type sensors with twin “fire” LED’s and anti-tamper security screws.
Temperature Sensors:
The temperature sensors installed were low profile analogue addressable type sensors with twin “fire” LED’s and anti-tamper security screws. The operating temperature of the sensor was set on site via the indicator control panel.
Alarm Sounder Bases:
The fire alarm sounder bases installed were low profile sounder base type and powered by the loop with a minimum of 90 dba at 1 metre to an IP rating of 32.
Alarm Sounder Beacons:
The sounders installed were wall mounted digital addressable type with an output of not less than 100dba at 1 metre.
Loop Isolators:
The system was complete with all loop isolators to suit the design requirements of the system. Where the system did not have loop isolation built into the detector or device then we installed one unit per 30 devices.
Interface Units:
We installed loop wired interface units comprising of input/output modules, change over relays, power supplies and all necessary monitoring equipment. We can confirm that these were installed to the following:
- Electronic retained doors (door access).
- Door hold opens.
- Mechanical control panels.
- Fire and fault signals
- All science lab gas controls.
Installation Work:
We can confirm that the installation was carried out utilising AEI Fire Tec Enhanced 2 core 1.5mm² screened separate earth conductor with an overall red LSF sheath fire cable installed in accordance with the various fire alarm loops indicated on the schematic diagram. Final connection to devices was carried out with proprietary cable glands and conduit boxes to provide a complete system. To allow smoke heat sensors to be fixed the cables were terminated via a conduit box fixed behind and through the ceiling to finish flush with the underside of the ceiling so that the sensors fix close to the ceiling, when terminating onto a device fixed to the suspended ceiling.
The fire alarm system was wired from the control panels on loops, sounders wired and powered by the loops. Circuit wiring for the loops was carried out using 2 core enhanced 1.5mm² cable. All circuit wiring was installed on existing trays/baskets, where possible, and “P” clipped direct to the fabric of the building elsewhere.
At the appropriate stage of the contract we provided the contractor a draft a schedule of equipment giving the proposed “address” zone, sensor, loop, location, text for display etc, with the assistance of the equipment manufacturer and submitted the schedule for comment to the Client through the Consulting Engineer.
We can confirm that this schedule was produced in sufficient time (minimum of 2 weeks) to allow it to be considered, commented upon and approved prior to the programming of the software for the system by the equipment manufacturer. We also protected all automatic sensors etc., from contamination by dust up to the time the fire alarm system is handed over to the Client.
Every device on the fire alarm system was fitted externally with a label, which provided the loop number to which the device is connected, the address of the device and the zone to which it is connected. In the case of automatic sensors two labels were fitted one to the base of the device and one to the head of the device.
During the execution of the works we produced marked up a set of drawings indicating the route taken by the loop wiring to the associated devices which assisted in the commissioning of the system.
The “As Fitted / Record Drawings” included line diagrams indicating the wiring arrangements, schematic diagrams and wiring diagrams indicating connection details. The reference given to each device are indicated on the record drawings. We also provided a loose leaf detailed Log Book which listed every device including sounders together with its address, identification, reference, type, location and where applicable the temperature setting of the device. The Log Book was made available in its final form for the “Hand Over” meeting and complied with the British Standard Specification.
Our panel manufacture installed all the necessary software and equipment into the fire alarm panel and carried out the testing and commissioning of both Installations. The tests included smoke and heat detector tests on all sensors in addition to the operation of the test facilities at all manual call points. The testing and commissioning was carried out in accordance with the British Standard Specification and Codes of Practice.
We can confirm that typed copies of the Testing & Commissioning Certificates were included within the Maintenance Manuals and a copy of each was sent to the Contract Administrator following the testing and commissioning operations.
We also provided and fixed a true to scale, framed, zone indicator location plan showing all zones adjacent to all the fire control panels and repeater panels. All rooms’ corridors and points of exit from the building were shown on the plan.
Soak Testing:
To enable the system to bed down following the installation the system was subjected to a full soak test for a period of 1 week. During this time the system was left in a no alarm state so as to indicate fire calls to the panels and initiate the relevant print outs.
During this period we were responsible for call outs to identify any spurious faults that have occurred on the system and investigate/report any faults on the system and provide a detailed report any remedial action required to the system. Any action required to the system during this period we completed as part of our contract.
Test & Commissioning:
The system was fully commissioned upon completion. All (new and existing) devices were then labelled as described previously. On completion of the works we provided all certification for each section of the works in strict compliance with BS 7671 and we issued the relevant certification as follows:
- Fire alarm completion certificate (NICEIC wiring)
- Fire alarm commissioning certification.
Maintenance Service Visits:
We also included the first year’s maintenance as prescribed by BS5839-1 & BS5255, with all results being recorded within the log books.
Commissioning & Instruction Attendance:
We can confirm that commissioning of all systems, witnessing and inspection was carried out prior to handover. This also allowed for the demonstration of the system and equipment to the client and their representative prior to contract completion.
Testing & Commissioning:
We can confirm that all testing and commissioning was carried out in accordance with the latest 18th Edition of the IEE Wiring Regulations.
Handover:
We can confirm that prior to handover all certification was completed and provided for checking by the Consulting Engineer 3 working days before handover. Once the Consulting Engineer approved these documents a full set of each was added into the Electrical O&M Manual these included the following information:
- NICEIC Electrical Installation Certificate.
- NICEIC Periodic Inspection & Test Certificate.
- NICEIC Emergency Lighting Completion, Design, Construction and the Verification Certificates.
- NICEIC Fire Alarm Completion, Design, Construction and Verification Certificates.
- NICEIC Fire Detection and Alarm System Acceptance Certificate.
Roller Shutters:
As part of the project we sub-contracted the supply and install 2 new internal Flameshield Fire Shutter from A1S Group. The Shutters are electrically operated, galvanised steel roller shutter to BS2989. This Included for all guide rails, endplates canopy/hood for coil when the shutters are in open position. We can confirm that the Shutter are controlled with a key switch. The 2 Roller Shutters were tested and commissioned to certify installation on completion.
We can confirm that the electrically operated roller shutters were connected to the main equipotential earth bonding, with an internal switch and fused spur located in a position agreed with the school. The 2 Roller Shutters were also wired into the Fire Alarm system and tested to ensure it operates when the fire alarm sounds. Include for audible alarm and light on descent.
Builders Work:
As part of the project we sub-contracted the replacement and repairs to approximately 85 x Fire Doors (FD30S Rating) these include for all External and Folding Doors. The builders works also included for the supply and installation of 8 x Internal Windows and associated making good works. We can confirm that these works also included treatment of fire compartmentation and all fire stopping works.
Project Timeline:
The project started on the 20th July 2023 with the main works being completed during the 6 Week Summer Holidays Period. We can confirm that additional works were carried out in the following half terms due school restrictions and access to some areas.
Mark Ruscoe – Senior Consultant, Arcadis Consulting (UK) Limited said the following:
‘We have worked alongside ASH Integrated Services on a number of various projects within the Education Environments where the programme of works/timelines are always very challenging, but they always deliver a good quality installation.’
‘The flexible approach and can do attitude of the ASH Team on site and the way they worked under pressure to get the project delivered on time was over and above expectations. We received so much positive feedback from the School Management and Maintenance Team about the ASH Team, where nothing was too much trouble.‘
The Benefit and Impact to St Joseph’s Catholic High School
We can confirm the benefit and impact to St Joseph’s Catholic High School are as follows:
- The long overdue investment and upgrade to Fire Life Safety Systems gave the School great comfort as one incident or accident away from being exposed.
- The project was carried out over the 6 Week Summer School Holiday Period and getting all works completed before the start of the new educational year was important to Schools image.
- The installation of new Fire Doors and Decorations carried out by the Building Team gave the School refresh which was appreciated by the pupils creating a much safer and improved environment to learn.
- There were some additional works to be carried out due to school restrictions and access to some areas. We returned to site during the next Half Term to complete these which didn’t impact on any of the pupils.
Lee Corbally – Electrical Project Manager, ASH Integrated Services said the following:
‘It was a very challenging project to manage as it was like 12 week job completed within 6 weeks’, we also had additional works to the project to complete and returned to site during the next half term. Communication was key and the working relationship with Mark Ruscoe – Senior Consultant who made this an enjoyable project to work on for all of us’.
Antony Grace – Director, ASH Integrated Services said the following:
‘I echo the previous comments made by my colleague Lee Corbally as the 6 week window to complete the project was challenging with our ASH Team working aways from home during the week to get this project completed on time.‘
‘We have carried out a number of these types of projects before, so know what obstacles and obstruction we can come across and how to overcome these. We were also delighted to get such positive feedback from the School Management and Maintenance Team and they were very supportive during the project.’
Since the project has been completed the Principle Consultant Arcadis Consulting (UK) Limited have invited ASH Integrated Services to tender for the Mechanical & Electrical Project Works at All Saints Primary School and St Phillips Primary School.
ASH Integrated Services are a ‘People Business’ and most importantly we invest in all of our team for the future. Through Apprenticeships and other vital industry qualifications to practical training, we ensure our team are upskilled, fully equipped and prepared.
We believe that when people are happy at work, they are more productive. Our in-house workforce, which accounts for ‘95 % of activity on-site’ and work the ASH Integrated Services way of being ‘Professional, Reliable and Friendly’.
Professional, reliable and friendly have become part of our embedded culture and become ASH Integrated Services ‘Core Values’.
Our self-delivery ability/capabilities, with a proven integrated solution are ‘Unique’ and our expertise in Mechanical, Electrical, FM Maintenance & Projects are as follows:
- Heating, Air Conditioning and Ventilation
- Gas/Combustion,
- Combined heat and power (CHP)
- Hot Water Systems, Chilled Water Systems, Plumbing and above Ground Drainage
- Electrical – Lighting, LED Lighting, Power (Single phase and three phase)
- Stand-by Systems (Uninterrupted power supply and generators)
- Data Points and BMS
- Renewable – Underfloor Heating, Hydrogen Boilers and Air Source Heat Pumps
- Renewable – PV Solar Panels, Battery Storage and Car Charging Points
ASH Integrated Services doesn’t stand still when delivering a truly integrated service led by our Directors Antony Grace, Sean Jackson and Howard Jackson. Not to mention our dedicated Management Team, Office Administration Team and all of our Engineers. As previously mentioned, ASH Integrated Services are a ‘People Business’ and we are proud of our (One Team) and integrated service delivery and also our ‘Accreditation’ which help provide St. Josephs’ Catholic High School with the necessary reassurance that they are in safe hands.