MHA Pennystone Care Home is a two-Story care home located in a Blackpool suburb. The facility is home to ‘36 Residents’ who continued to occupy the home throughout the Mechanical and Electrical Installation Project.
The home consists of assisted living where residents have individual rooms and communal living facilities including commercial cooking and common lounge and dining areas.
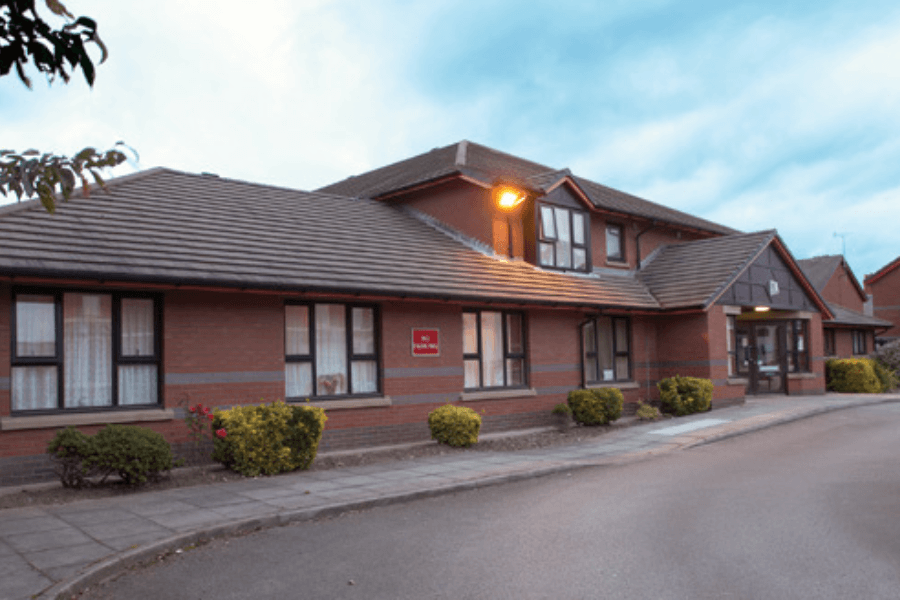
Multi Award Winning ASH Integrated Services fully respect, understand the sensitivity and priority of the care home environment. We already have a number of care homes under our remit with other clients and this provided MHA Pennystone Care Homes with the reassurance that we could not only support, but understood the needs of all their residents during this important Mechanical and Electrical Project.
Please Note: This was a phased replacement of services to limit implications on occupants during the replacement works and allowing occupation of the building.
ASH Integrated Services offers a joined up electrical, plumbing, heating, air conditioning and renewable energy project and maintenance solution, which reduces stress for clients by offering one point of contact and dedicated mechanical and electrical supervisors on each contract/project.
Principle Contractor:
These works were originally tendered via Jin Kooner – Contract Director, CLC who were the Principle Contractors for the project. We have previously carried out successful project works with CLC at the Ministry of Defence (MOD) and also for Staycity Aparthotels. Since then we now have a national contract for Mechanical & Electrical PPM/Servicing and Project Works direct with Staycity.
Projects and Project Management is a prime focus and area of competence within ASH Integrated Services where we have previously carried out similar successfully Replacement Mechanical & Electrical Projects for our clients. We recognised an element of this project needed be delivered by Sub-Contractors such as BMS Control Systems, Fire Alarms Systems, Builders Works/Making Good and work related to the Website Monitoring. Although we always aim to ‘Self-Deliver’ as many services as possible, using our directly employed Engineering Team. This helps us to keep costs under control and provide a consistently high level of quality and ‘First Class Service’.
Working alongside and with our Sub-Contractors as ‘One Team’ we successfully delivered all aspects of the project, including design and build, installation and also maintenance if required after the project was completed.
Extent of Works – Mechanical Building Services:
Domestic Hot Water:
We undertook and developed the technical design, supply, installation, test and commission of the domestic water services systems. We installed a new Domestic Return Circulating Pump. The pump was monitored at the Main Controls via Differential Pressure Switch and notified failure to the control panel.
We then supplied and installed 2 No new Calorifiers (electric heated) along with new cold-water booster set replacing the existing 2 No electric hot water calorifiers located within the existing plantroom on a like for like basis. With the existing calorifiers within the plant room isolated, decommissioned and stripped out and appropriately disposed of. We created a new concrete bases for the new water booster set and calorifiers. The 2 No new Calorifiers were then installed and connected to the Hot Water System to allow for a minimum of 10 minutes of peak capacity hot water usage. Pipework connections were then provided equally to both vessels so to share the duty of the system with new secondary circulation pump and all other valves and ancillaries were installed to set the new domestic services.
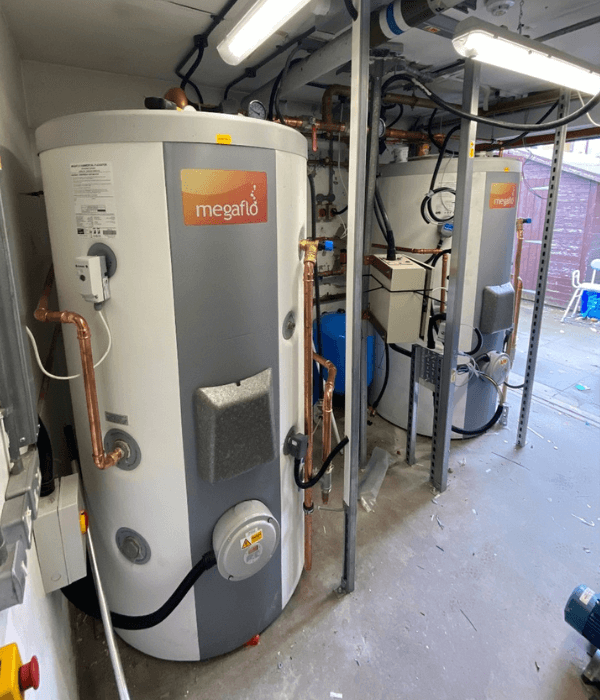
The new Hot and Cold Water Services were then installed throughout the building to serve the existing sanitaryware. Where existing sanitaryware positions are being relocated, existing hot and cold water were also modified as required to suit the new position. Wash hand basin outlets were also installed with TMV3 Thermostatic Mixing Valve to limit outlet temperature to 43 degrees C.
Domestic Cold Water:
This was installed put into operation and commissioned to achieve the required flowrates. The existing Cold Water Service Tanks were then stripped out and replaced one at a time to limit interruptions to service provision. With a new Domestic Hot Water service and Secondary Return Pump installed to circulate heat throughout the domestic services distribution.
We can confirm that the replacement of the entire hot and cold water system was carried out in phases to allow resident occupation of the facility throughout the works. The new Cold Feed Tanks were installed on a like for like basis, complete to current regulations; we also re-routed the warning pipes to the external location to indicate visible problem, with the overflow connected to the existing drain.
A new Booster Set was installed complete with Duty/Standby Jockey Pump Sets. External Bib Taps with Category 5 Pipe Interrupter with Ball Float Valve and overflow arrangement were also installed. All pipework installed was also insulated so to be protected from freezing at temperatures of down to -15oC. Where there was a resultant risk of pipework freezing then Trace Heating was installed and insulated using self-regulating systems.
Domestic Pipework & General:
We can confirm that all Hot and Cold Water Services were suitably insulated and boxed where appropriate. The water fittings and equipment installed were Water Regulations Advisory Scheme (WRAS) approved. The water services were also designed in accordance with BS EN 806 and the Institute of Plumbing Design Guides.
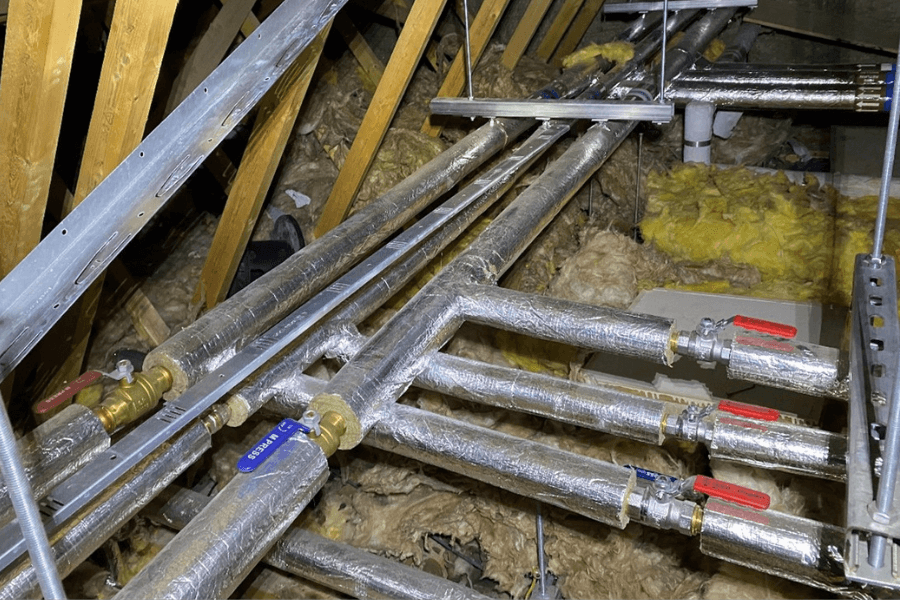
All pipework installed was Copper Half Hard Table X, with lead free solder or brazed connections. All pipework was also thoroughly flushed and cleaned prior to being charged with water for pressure testing. Then tested to a One Point Five multiplier [1.5x] times operating pressure or Eight [8.0] bar, whichever was the greater.
Prior to hand over a Total Volatile (TVC) Count was carried out at two locations on the system. We then removed all redundant equipment from site and disposed of appropriately.
Metering:
We also supplied and installed a Water Meter supplying the Calorifiers and a Mains Water Check Meter and these were connected to the Control Panel.
Heating System:
We undertook and developed the technical design, supply, installation, test and commission of the heating systems. The radiators supplied were the same manufacture as the existing installation and replaced in phases to allow occupation of the building.
We supplied and installed new Electric Radiators throughout the Care Home and where existing radiator positions are to be relocated, the existing radiator position and walls were made good and redecorated. Each radiator was provided with individual local control via radio frequency wall mounted controllers and its own switched fused connection unit.
The existing Cooling (DX) systems were retained and we ensured the system was protected and remained fully operational for the duration of the works.
Controls/Building Monitoring and Management System:
We undertook and developed the technical design, supply, installation, test and commission of the Control System to provide a like for like system as the existing installation. New manufacturers packaged controls were installed with all new plant to give control of the equipment. We can confirm that the new Controls System was commissioned by manufacturers approved specialist.
Extent of Works – Electrical Building Services:
Low Voltage Distribution Systems:
We can confirm that a new LV Distribution was installed as per the specific services layouts drawings, allowing for phase working to avoid any unnecessary loss of power for any part of the building. All planed disconnection, changeover of supplies were always agreed with the client team at least 7 days prior to work taking place.
All existing distribution boards to be fully operational until final circuits have been connected and tested to new DB’s. All new Distribution Boards were suitably sized in terms of ways for all final circuits and complete with 20% spare ways
We undertook the technical design proposal including sub and final circuits and devices for outgoing ways and a Full Validation Survey was undertaken with the Electrical Installation Condition Report (EICR) was verified prior to submitting our final design. All circuits feeding socket outlets were equipped with Arc Fault Detection Devices (AFDD) and all outgoing ways except those listed and circuits feeding fridges, freezers and any equipment which may cause nuisance were RCBO’s protected.
We can confirm that where RCD/RCBO earth fault protection was used for circuits, the maximum permitted Zs of the circuit to achieve the disconnection times set out in BS 7671 was that of the MCB, not the RCD element. The RCD was for additional earth fault protection only and must not be relied upon to achieve the disconnection times in relation to Zs, this must be achieved by the main overcurrent protective device alone.
All heating distribution boards were fed via contactors located within the electrical room. Distribution boards were mounted so that they are readily accessible and fixed firmly to the building fabric or to metal framework by nuts, bolts, washers and in maintainable locations accessible without use of access equipment.
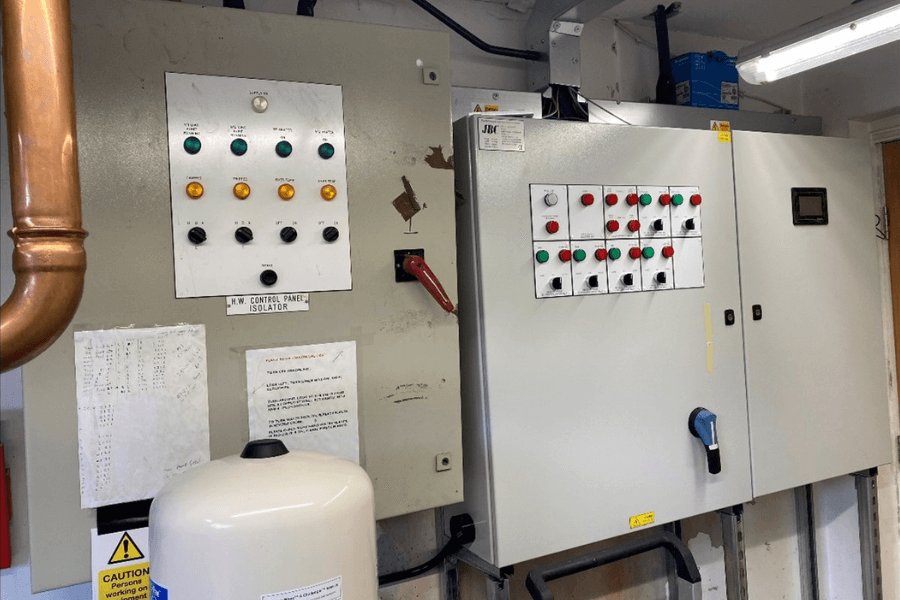
Distribution boards were supplied complete with integral two or four pole mains isolator with cable terminations sized to accommodate the specified supply cables. Distribution boards supplied were complete with fully rated neutral and earth termination with one neutral and earth connection for each single phase output distribution way. Distribution boards came complete with adequate earth termination facilities to accommodate the equipotential and supplementary earth requirements. We also ensured that the positioning of distribution boards would allow full accessibility for future maintenance.
We can confirm that all circuit ways were clearly identified with the distribution schedule are displayed in a suitable plastic pocket accordingly for the new distribution boards. We can also confirm that a copy of the site wide electrical schematic was left on site at the mains position and laminated.
All final circuit cabling was LSZH with all switchgear installed in accordance with the specification – Fully Type Tested Assemblies (TTA) to BS EN 60439 complying with the recommendations of the relevant Design Standards.
The sub main cabling was XLPE/LSF/SWA/LSF multi-core with separate green/yellow sheathed circuit protective conductors. Sub main cabling run was affixed to steel galvanised cable tray systems. All cabling was affixed with non-flammable fixings.
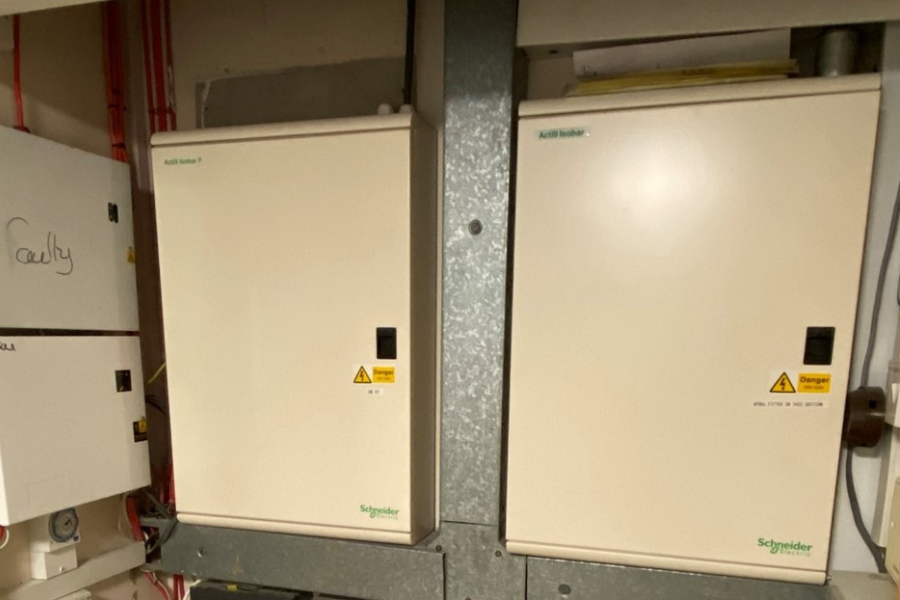
All supplies associated with the operation of systems under fire conditions was wired using appropriately selected fire rated cabling and supported on cable tray having a fire rating of 2hrs. The steel also supports a maximum stress of 10N/mm2/ in accordance with BS 8519 Annex E.
The sub-main cabling was fully identified along their entire length with the LV distribution asset reference, with all cables provided by the same manufacturer. We can confirm that the cable ends cut on site which are not to be terminated immediately were sealed. All cable ends were sealed upon completion of tests. Allowance was also made for expansion joints in long runs. The cables were also laid in multiple runs so that minimal crossing of cables occurs.
We can confirm that armoured sub main cables installed was compliant with BS 7671. All cable types and specifications installed were suitable for the environmental conditions which the cables will encounter in service. All multiple cables were also fixed to cable tray/cable hanger/support systems.
With ingress protection at a minimum of IP31 rating and all cable entries into the board to maintain this protection rating. All terminations were fully shrouded. Access to busbars and cabling terminals can only be by removal of fixed screwed cover plates. Distribution boards were complete with lockable hinged front covers (side hinge only) to provide access to fuses, Miniature Circuit Breaker (MCB)s and Residual Current Device (RCD)s for maintenance and switching. We also provided a fixed circuit charts shall be within each distribution board.
All final circuit cabling was LSF single core cabling in multi compartment trunking and rigid conduit systems throughout. With all trunking lids steel galvanised finish to match the main containment system(s). We can confirm that all cabling was contained within rigid steel galvanised conduit. Our cable sizing takes in account the maximum continuous current rating, voltage drop in the sub main circuit and maximum circuit impedance for the operation of short circuit and earth fault protective devices.
The containment systems was mounted via strut and drop rods and installed in accordance with BS7671. The containment systems offers a min. of 20% spare capacity. Wiring in escape routes was supported and not be liable to premature collapse in the event of fire. All containment was supported using metal fixings and cable and held in metal containment systems and mounted in the horizontal plane. We can confirm that all works complied fully with the requirements of BS 76713.
Electricity Metering Systems:
As part of the requirements of The Building Regulations Part L in respect of energy metering and compliance with The Building Regulations and specifically Part L2 we provided energy metering to assign at least 90% of the estimated annual energy consumption of each fuel (in this case electricity) associated with the LV switch gear panels that formed part of our scope of work.
The metering provided separately and directly displayed and recorded the following:
- General lighting distribution boards
- LV power distribution boards
- Any major power using equipment.
Mains Power Supply Transient Overvoltage:
We can confirm that Type 2 panel mounted (integral) surge suppression devices were provided for electrical distribution equipment and busbars. Type 3 devices were installed for data transmission and warden call/nurse call and all other sensitive equipment. TVSS devices were incorporated within all main and sub distribution network LV switchgear panels and those supplying circuits externally to the building envelope. The systems was hard wired 3-Phase, 4-Wire, 50/60Hz plus neutral. TVSS devices were installed to prevent from electric power surges and spikes. Audible failure alarm were provided and thermal overload protection was installed with a maximum surge current rating for each device selected to suit the application. LED status indicators for each phase and an audible alarm for immediate failure notification when suppression circuitry has been damaged by a heavy strike or surge. Outgoing ways within the main and sub distribution LV switchgear boards was installed and suitably rated to feed the new integral TVSS.
Hardwired General Lighting Systems:
We can confirm that a new general lighting system was installed. The lighting was selected on the basis of LED luminaires and a sample of each and every luminaire provided to the client review. The general lighting system was designed to suit the guidance as described in CIBSE Lighting Guide 9 and suitable for use within the care environment. All new lighting had integrated wireless programming capacity to allow for contract monitoring and fault reporting. All systems were based on mesh systems rather than Bluetooth based communication.
We can confirm that all luminaires and scene set control were installed to the following area(s):
- Meeting Rooms
- Lounges
- Community rooms.
- Dining rooms
- Chapels and prayer rooms.
We can confirm that presence detection control were installed to the following area(s):
- WCs.
- Bathrooms (min 10min timer)
Presence/absence detection with step back (10%) were installed to the following area(s):
- Corridors / circulation
Absence detection control were installed shall to the following area(s):
- Offices
- Plantrooms.
Local switch control were also installed to the following area(s):
- Kitchens.
We can confirm that all automatic lighting control was installed with manual key switch override. Generally, all lights in circulation areas controlled by presence detection remained on at 10% as a base lighting level throughout, the fittings should then ‘ramp’ up to full output on occupancy detection. The luminaires are also controlled by build in controllers/detectors. The general lighting offers control and power circuits to increase the flexibility of the space/zone control and fed from new final circuits throughout supplied from the landlord LV distribution board.
Small Power Systems:
We can confirm that a small new power system was installed, including switched socket outlets and data points. Allowance was made to allow for power supply to warden call/nurse call system. Cleaner’s sockets were installed and spaced for coverage with a 5m radii i.e. 10m centres throughout the extension. With 4no. double switched socket outlets and 3no. switched fused connection units at each residents’ bedrooms.
All accessory mounting heights were in accordance with the requirements of Building Regulations Part M, BS 8300 and the Equality Act as well as with client requirements to accommodate operational needs for staff and clients.
We can confirm that all works comply fully with the requirements of BS7671. The accessories were also labelled with their circuit reference and all fused connection units were labelled stating the connected equipment. We then tested and commissioning of the completed system. All small power accessories for general use in plant rooms, boiler rooms etc. including light switches, socket outlets (to IP44) were selected in accordance with The Equality Act.
Small power was installed the following equipment:
- Dishwashers
- Fridge/Freezers
- Water boilers
- HVAC equipment
- Access Control.
We can confirm that all exposed electrical accessories within plant spaces were provided with a Traffolyte label identifying the final circuit reference and the purpose of the final socket outlet/supply/final circuit for ease of small power identification.
Emergency Lighting:
We can confirm that the emergency lighting system was installed thought the building to provide lux levels required in BS 5266. The emergency lighting was selected on the basis of LED luminaires. All emergency luminaires have green LED’s for operational. The emergency lighting installation provides 3 hours of non-maintained emergency illumination and on the basis of integral 3hr battery packs within standard luminaires or standalone LED emergency luminaires.
The emergency luminaires are self-contained LED type, capable of communicating status via the wireless mesh network to the Gateway. With the system test times and other parameters programmed via the website, the information is automatically downloaded to the Gateway. The Gateway controls all emergency testing and reporting automatically.
Website System Monitoring:
We can confirm that all luminaires report status to the Gateway once per day. This will include failure status, energy performance data, occupancy profile and air quality information. These records are uploaded to a website periodically where the data will be stored securely and displayed in graphical format. The website also store supporting site documentation including all as fitted drawings, interactive drawings, commissioning certificates and any other documentation required by the end user.
The luminaires specified with integral self-test emergency lighting function do not require local emergency lighting test key switches for means of testing, however a detailed and proposed testing methodology was completed and issued within the O&M Manuals, TM31 Log Book, Building User Guide and formed part of the end-user hand-over training.
Clear labelling of the circuit reference and luminaire locations are also applied complete with an asset register of emergency luminaires. This document also formed part of the O&M Manual. We also carried out a demonstration of the complete system to the Fire Officer, Building User, Client and Engineer at handover and close out.
Included in the O&M Manual regarding the emergency lighting installation:
- Certificate of design, installation, verification and commissioning
- Test certificate.
- Log books.
- Asset register.
External Lighting Systems:
We can confirm that new external lighting was installed. The lighting selected on the basis of LED luminaires. The external lighting was wall mounted and provided to cover all external walkways, entrances car parks and sitting areas. The external lighting was fed from final circuits emanating from the dedicated external lighting local LV distribution board(s). All external lighting are provided with photocell and also time clock controlled.
Nurse Call System:
The client incumbent system provider carried out the design and supply/install new nurse call system. Power supply for nurse call system were limited to maximum 4 per circuit. With all circuits 2.5mm T&E LST radial type and supplied via 6A RCBO’s from local DB’s. Allowance were made for 2 no. double and 1 no. single sockets outlets for UPS, router and data cabinet to electrical riser 1.
Fire Detection and Fire Alarm System:
The existing fire detection and alarm system was replaced in 2016 and as part of this project we carried out the test and validate of the existing system to ensure it complied fully with the requirements of BS 5839-1.
Earthing and Bonding Systems:
We can confirm that new earthing and bonding was installed throughout and complied with Requirements for Electrical Installations IET Wiring Regulations Eighteenth Edition BS 76716 and BS 74307 Code of Practice for Earthing.
The earthing and bonding of the electrical installation included the following:
- The frames of equipment forming part of the electrical installation, conduit, trunking and cable sheaths were sufficient supplementary bonding, so as to form a continuous path to earth.
- All extraneous metalwork within the plant were properly bonded to earth by means of earth cabling. Earth connections were crimp type lugs bolted to metalwork.
- All extraneous metal work throughout the building. Including pipework and ductwork.
Project Timeline:
The project started on the 15th September 2023 and was completed on the 31st March 2024, with the works being carried out in different phases which took approximately 28 Weeks to final completion.
Jin Kooner – Contract Director CLC said the following:
‘All at MHA Pennystone Care Homes were delighted to have ASH Integrated Services on board. The working relationship and understanding the importance of the Care Home Environment provided them with great comfort.’
‘ The quality of the Project Work and the ASH Team on site has really been First Class, we look forward to working with ASH Integrated Services again’
The Benefit and Impact to MHA Pennystone Care Homes
We can confirm the benefit and impact to MHA Pennystone Care Homes are as follows:
- It is not just the care of Residents and Day Visitors that is a priority of MHA Pennystone Care Homes, but the ’Importance of the Environment & Conditions’ with the loss of power, heating or hot water, which can have a major impact and risk towards their care.
- The care environment is highly regulated, with the home receiving regular unscheduled checks from both the care sector and environmental regulatory bodies. As such, the home needed to be inspection-ready at all times and the benefit of the project will support this.
- Because we carried out the work in phases and over a 28 Week Period there was no disruption to the day to Day Care of the 36 Residents living at the home. We also programme in our out Team and sub-contractors accordingly, so site wasn’t flooded with labour at any one time.
- With ‘Fuel Costs’ rising astronomically having energy efficient reliable services will have a big impact and benefit to MHA Pennington Care Homes for years to come.
Howard Jackson – Director, ASH Integrated Services said the following:
‘SME’s like ASH Integrated Services play an important part of the FM/Engineering Sector as certain works like at Pennystone Care Home may not be deemed the most attractive to the larger FM/Engineering Service Providers’.
‘But they are the life blood of SME’s like ASH Integrated Services in an environment where we excel and where we are best placed to deliver’.
Since the project has been completed the Principle Contractor CLC have invited ASH Integrated Services have been invited to tender for the Mechanical & Electrical Project Works at Ashberry House Care Home.
ASH Integrated Services are a ‘People Business’ and most importantly we invest in all of our team for the future. Through Apprenticeships and other vital industry qualifications to practical training, we ensure our team are upskilled, fully equipped and prepared.
We believe that when people are happy at work, they are more productive. Our in-house workforce, which accounts for ‘95 % of activity on-site’ and work the ASH Integrated Services way of being ‘Professional, Reliable and Friendly’.
Professional, reliable and friendly have become part of our embedded culture and become ASH Integrated Services ‘Core Values’.
Our self-delivery ability/capabilities, with a proven integrated solution are ‘Unique’ and our expertise in Mechanical, Electrical, FM Maintenance & Projects are as follows:
- Heating, Air Conditioning and Ventilation
- Gas/Combustion,
- Combined heat and power (CHP)
- Hot Water Systems, Chilled Water Systems, Plumbing and above Ground Drainage
- Electrical – Lighting, LED Lighting, Power (Single phase and three phase)
- Stand-by Systems (Uninterrupted power supply and generators)
- Data Points and BMS
- Renewable – Underfloor Heating, Hydrogen Boilers and Air Source Heat Pumps
- Renewable – PV Solar Panels, Battery Storage and Car Charging Points
ASH Integrated Services doesn’t stand still when delivering a truly integrated service led by our Directors Antony Grace, Sean Jackson and Howard Jackson. Not to mention our dedicated Management Team, Office Administration Team and all of our Engineers. As previously mentioned, ASH Integrated Services are a ‘People Business’ and we are proud of our (One Team) and integrated service delivery and also our ‘Accreditation’ which help provide MHA Pennystone Care Home with the necessary reassurance that they are in safe hands.